Secciones |
---|
|
| Foros Electrónica |
---|
|
| Alguien dijo ... |
---|
Si buscas resultados distintos, no hagas siempre lo mismo,
Albert Eisntein(1879-1955). Físico alemán. Premio Nobel de Física 1921. | Contacto |
---|
|
| TI CONTROLLERS AND TIER ELECTRONICS BOOST WHITE GOODS' EFFICIENCY BY UP TO 30% | | | |
DALLAS – As fuel prices and electric power rates continue to climb, the incentives for energy savings have never been greater. Embracing this opportunity for conservation, Tier Electronics LLC and Texas Instruments Incorporated (TI) (NYSE:TXN) today announced that TI's digital signal processing- (DSP) based TMS320C2000™ controllers are the key component in Tier’s motor control system for washing machines and other white goods. System designers using Tier’s Mini Universal Power Converter (UPC) can harness the processing power and efficiency of TI’s C2000™ controller that, when combined with Intelligent Power Modules (IPM) and pressure-stamped heat sinks, can reduce costs by up to 25% by halving component counts and can deliver up to 30% better efficiency compared to conventional microcontroller (MCU) or discrete-based designs. The reduction in parts count will also improve MTBF (mean time between failure) ratings.
Efficient Design Delivers Impressive Results
Many of today’s white goods use conventional single phase motors that require simple control algorithms and hardware, but are noisy, bulky and waste energy. To avoid this problem, designers have to maximize efficiency, making sure that motors are used to the fullest extent in order to minimize the amount of power wasted. The UPC design integrates TI's C2000 controller, enabling use of a multi-phase alternating current (AC) motor that can be controlled with an adaptive-based field oriented control (AFOC). Multi-phase AC motors controlled with an adaptive algorithm are smaller, run more quietly and provide precise speed and torque control based on a machine's load to avoid wasting energy. The AFOC scheme strives to maintain an angle between the rotor flux and the stator flux that is optimized to improve motor efficiencies, while actively controlling the torque, therefore significantly improving overall performance. The AFOC vector control reduces the voltage and current peaks and valleys associated with scalar and traditional FOC control, which also produces quieter appliances.
Additionally, digital signal controllers provide improved pulse width modulation (PWM) control compared to conventional control systems, keeping a motor’s total harmonic distortion (THD) at a minimum over a wide operating range. This also leads to lower operating temperatures, higher efficiency, better power factor ratings and lower materials costs, especially in regards to the amount of copper required for the motor. The digital signal controller’s ability to produce cleaner waveforms translates into the ability to use a motor that is smaller and does not need external sensors.
In addition to utilizing the powerful computing capabilities of TI's C2000 controllers, Tier employed innovative technologies to achieve its advanced motor controller design. Intelligent Power Module (IPM) technology reduces Bill of Material (BOM) and manufacturing costs with its high level of integration of components including insulated gate bipolar transistors (IGBTs) and free wheel diodes. Advanced built-in protection is another feature of the IPM which improves reliability by up to 30%. Pressure-stamped heat sinks round out the motor control system’s triple play. They use a procedure of cold extruding solid aluminum pieces into precise shapes in a single process. They are less costly to manufacture and deliver superior heat dissipation compared to conventional heat sinks.
DSP Power and Performance + MCU Peripherals = Success
“We determined early on that TI’s C2000 controllers were the only product that met all of our requirements. These devices provided the number-crunching capability necessary for AFOC control along with enough headroom to integrate advanced features like power factor correction, motion profiling and spread spectrum PWM generation,” said Jeff Reichard, CEO, Tier Electronics LLC. “Having a motor control platform that is reprogrammable in software allowed for easy tweaking or adjustment of systems to increase efficiency or enable system re-use with different motor types.”
TI's 16-bit TMS320F24x™ fixed-point DSP-based controller provides up to 40 MIPS of performance and features an integrated single-cycle multiplier, seven pulse width modulation (PWM) variable frequency and dead-time ports, five or more ultra-rapid 10-bit analog to digital converters (ADCs), an impulse capture circuit with a 16-bit timer and asynchronous serial communication. Integrated Flash memory allows re-programmability during the development phase and in the field, which satisfies low cost constraints and speeds time to market. A low cost, pin compatible ROM version designed specifically for appliance applications is also available. |
Jueves, 01 Junio, 2006 - 03:20 |
| 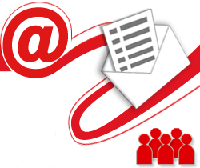 |
| |